View this article as PDF
Practical Guide To Arc Flash and NFPA 70E
By: Daryn Lewellyn
I began my first job in electrical maintenance when I was hired in at Terre Haute Malleable and Manufacturing Company in 1984; a long-since-closed iron foundry in Terre Haute, Indiana. It was a one-hundred-year-old facility, dark, with dirt floors made of sand and coal dust and known by the workers as The Malleable. Some of my most memorable work experiences happened in the four short months I worked there. I remember not receiving any electrical safety training.
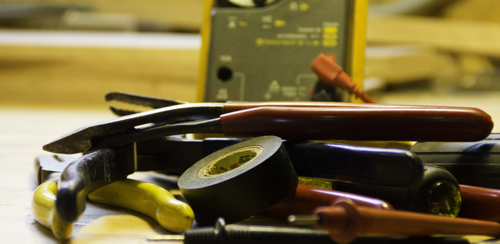
I remember when an older electrician named Bill gave me the arc flash training. It wasn’t called arc flash training because none of us had ever heard that phrase before. We didn’t know what happened when panels blew up or that it had a name. The information was given as somber advice while we were standing in front of a large disconnect. Bill said, “When you open or close one of these big disconnects don’t stand in front of it. Stand off to the side, use your left hand, turn your head and it might not hurt to duck a little.” I asked why and he said, “sometimes these things blow up.” That was good advice then and is still relevant today. The problem was that in 1984 that advice was the entire arc flash class. That was all we knew. Several years later I was repairing a variable frequency drive when part of it exploded when I closed the breaker. I was standing off to the side and was not injured. Thanks, Bill.
Thirty years ago we wrapped electrical tape around screwdrivers and called them insulated. We thought the plastic dipped handles on our Klein lineman’s pliers made them safe. Channel locks were fuse pullers. We wore polyester shirts and gold chains, and our only PPE was a hard hat, steel-toed shoes and safety glasses.
A lot has changed in regards to electrical safety and electrical safety training in the decades since. Arc-rated clothing has replaced our polyester shirts, voltage-rated insulated tools have replaced electrical tape, and most importantly, awareness of electrical hazards has replaced our ignorance. We can no longer work as we did back then, and we have to receive training on electrical hazards. In the ten years, I worked in factories, my employer never gave me formal electrical safety training. The first electrical safety class I was a part of I was the instructor.
In this Practical Guide To Arc Flash and NFPA 70E, I hope to simplify parts of the standard. This guide is not going to answer every question you have, and it doesn’t address every article in 70E. What I am hoping to accomplish with this guide is to help you understand the standards’ most impactful sections and to give you guidance on whether your facility needs more work on your overall electrical safety program.
As I travel the country providing 70E training and consulting for my clients, I have recognized a need for a guide like this. I wrote this guide for qualified workers, managers, and supervisors to assist them in making people safer while working around electrical hazards. Whether you call the training electrical safety training, 70E training, or arc flash training, it is a good idea to read this guide first as it may generate some good questions to have clarified during your training.
Access To The 70E Standard
Every facility, company or organization needs an easily accessible copy of 70E. I like the pdf version because it’s searchable and you can access it over a network.
I also think the 70E Handbook is a handy tool. It has interpretations, explanations and added material, not in the 70E standard. The Handbook can be purchased as an eBook and read on a tablet, Kindle or your phone. Wherever I am, I have 70E and the handbook on my phone. I also keep the OSHA regulations 1910.301 – 308, 1910.331 – 335, and 1910.399 at my fingertips, and all searchable.
Electrical Safety Responsibilities
Both OSHA and 70E agree on what the employers’ and the employees’ responsibilities are when it comes to electrical safety. Both require the employer to establish, implement, and document electrical safe work practices and procedures. And to train their employees on them. The employee’s responsibility is to comply with these work practices. These work practices will include many things, such as de-energizing equipment, PPE, risk assessments, approach boundaries, etc. The priority of these work practices must be the elimination of the hazard. De-energize the circuit, use the live-dead-live test to verify that it is de-energized.
Using arguments like we can’t afford the downtime, production won’t let us shut it down, and the boss or client say’s we have to work live, do not work anymore. These things are money issues and have no place in the decision-making process when we are de-energizing equipment. When a facility decides to work energized because it might save money they needlessly put workers in a possibly fatal situation. The world will not end if you experience a short downtime.
Exposure To Electrical Hazards
If a worker is about to begin a task that will be exposing them to electrical hazards a few things need to be clear. First, the worker has to be qualified for the work they are about to undertake. They must be able to demonstrate that they understand the equipment operation and construction, have received training on the hazards present, and have been trained on how to reduce the associated risks. The employer must document when the qualified worker received electrical safety training and the contents of that training when they demonstrated their proficiency with the work practices, and retain the documentation for the duration of their employment.
A helpful way to prepare for this is to imagine OSHA walking into your facility and asking if the worker they see using a voltmeter is qualified for the work they are doing. How would you answer and what documentation would you be able to provide to make your case?
Next, assuming we have determined the worker is qualified, we need to look at the task they are about to perform. Let us use as an example of adding a circuit breaker to a 480/277 volt panel-board labeled “Panel-A.” OSHA and 70E agree that we can’t do this work energized. Thirty years ago we may have inserted or removed a circuit breaker while the panel was live. But not today.
OSHA and 70E both require circuits above 50 volts be de-energized before work proceeding. Unless de-energizing would cause increased or additional hazards, such as life support systems at a hospital, or alarm systems. We are also allowed to work energized if it is infeasible to de-energize the circuit. I can tell you OSHA doesn’t believe many things are infeasible. Measuring voltage during the commissioning and startup equipment, measuring voltage and current during troubleshooting, for example, are allowed because it is infeasible to measure voltage and current if the circuit is de-energized. Just because it is acceptable doesn’t mean you have to permit it. Many companies do not. We may also have to work de-energized on circuits below 50 volts if they present a potential arc flash hazard.
OSHA requires you to work energized in one critical task. Lockout/Tagout. One of the steps of LOTO is verifying you have zero volts on the circuit you just de-energized. You must consider every conductor energized until you verify zero energy. When you are validating zero voltage, we have to regard this as live work. What if you opened the wrong disconnect. That happens all of the time. Perhaps the most important things we preach to our clients is, “Test Before Touch,” and, of course, wear PPE while you’re doing it. Every circuit has to treated as energized until we have proven it is not.
Job Safety Planning
Before a task has begun that will expose workers to electrical hazards, such as our example of adding a circuit breaker to a 480/277 volt panel, a qualified person must create a job safety plan(JSP). The JSP has to include a description of the job and tasks, shock and arc risk assessments, and work procedures, special precautions, and energy controls. Once you have the plan created a job briefing needs to take place. Annex I of 70E has a helpful job briefing and planning checklist.
Approach Boundaries
Your electrical safety training must stress these boundaries, so every qualified fully understands what they mean. Approach boundaries operate as their name implies; as you approach a piece of electrical equipment with exposed energized circuit parts, there is a point at which the risk of injury becomes great enough that additional rules apply. Two shock-protection approach boundaries will be a central part of your shock protection; those are limited and restricted. They each have their own rules. There is also an arc flash boundary that marks where a second-degree burn is likely to occur on bare skin if an arc flash occurs. Each of these boundaries marks a spot where an increase in awareness, blocking access, work permits and PPE are going to be required. These boundaries mark the line where the likelihood of an injury and it’s severity increase. Barricades, an attendant, or tape are needed to identify the first encountered boundary.
The Limited Approach Boundary
The limited approach boundary is a distance from the employee to an exposed energized circuit part within which a shock hazard exists. The typical nominal AC voltages that a maintenance person would be working on of 120, 208, 220, 240, 277, 380, and 480 all have a limited approach boundary of 42 inches. For higher voltages, please refer to the latest edition of 70E. No unqualified person is allowed inside the limited approach boundary unless a qualified person is escorting them. Crossing this invisible boundary triggers the need to establish an electrically safe work condition.
Electrically Safe Work Condition (ESWC)
You have established an ESWC when you have disconnected the equipment, locked and tagged the disconnect, tested to verify an absence of voltage, and, if necessary, temporarily grounded the equipment. The temporary ground is something typically used in circuits above 1000 volts.
Restricted Approach Boundary
This boundary triggers the need to insulate the worker from the exposed circuit parts by utilizing insulated rubber gloves, insulated tools, sleeves, shields, etc. Unqualified workers are not allowed within the restricted boundary or to take any conductive material or tool within this boundary. There is no listed restricted boundary for 120 volts AC, 70E says to avoid contact. You must wear insulated gloves, use insulated tools when contacting live 120-volt circuits. The earlier mentioned voltages of 208, 220, 240, 277, 380, and 480 volts AC have a restricted boundary of 12 inches.
Arc Flash Boundary
This boundary is a distance at which a worker could suffer a 2nd-degree burn in 1 second to exposed bare skin. We must utilize proper PPE for arc flash protection when inside this boundary. The arc flash boundary is independent of the shock protection boundaries. Where your restricted and limited shock boundaries are 12 inches and 42 inches respectively, the arc flash boundary might be 50 feet, or it might be 1 inch.
Shock risk assessment
We have to perform a shock risk assessment, starting with identifying the shock hazard, which in the example of adding the circuit breaker will be 480 volts. We know our limited approach boundary will be 42 inches and the restricted 12. We will need to de-energize the upstream circuit breaker that feeds “Panel A.”
Turning off the main circuit breaker of “Panel-A” de-energizes all of the circuit breakers in “Panel-A,” but it does not de-energize “Panel-A.” A common misconception. The line side, the side of the breaker with the incoming power, normally the top of the breaker, will still have 480 volts even when turned off. A shock and arc flash hazard would still be present. To de-energize “Panel-A”, we will need to go to the upstream circuit breaker that feeds “Panel-A.”
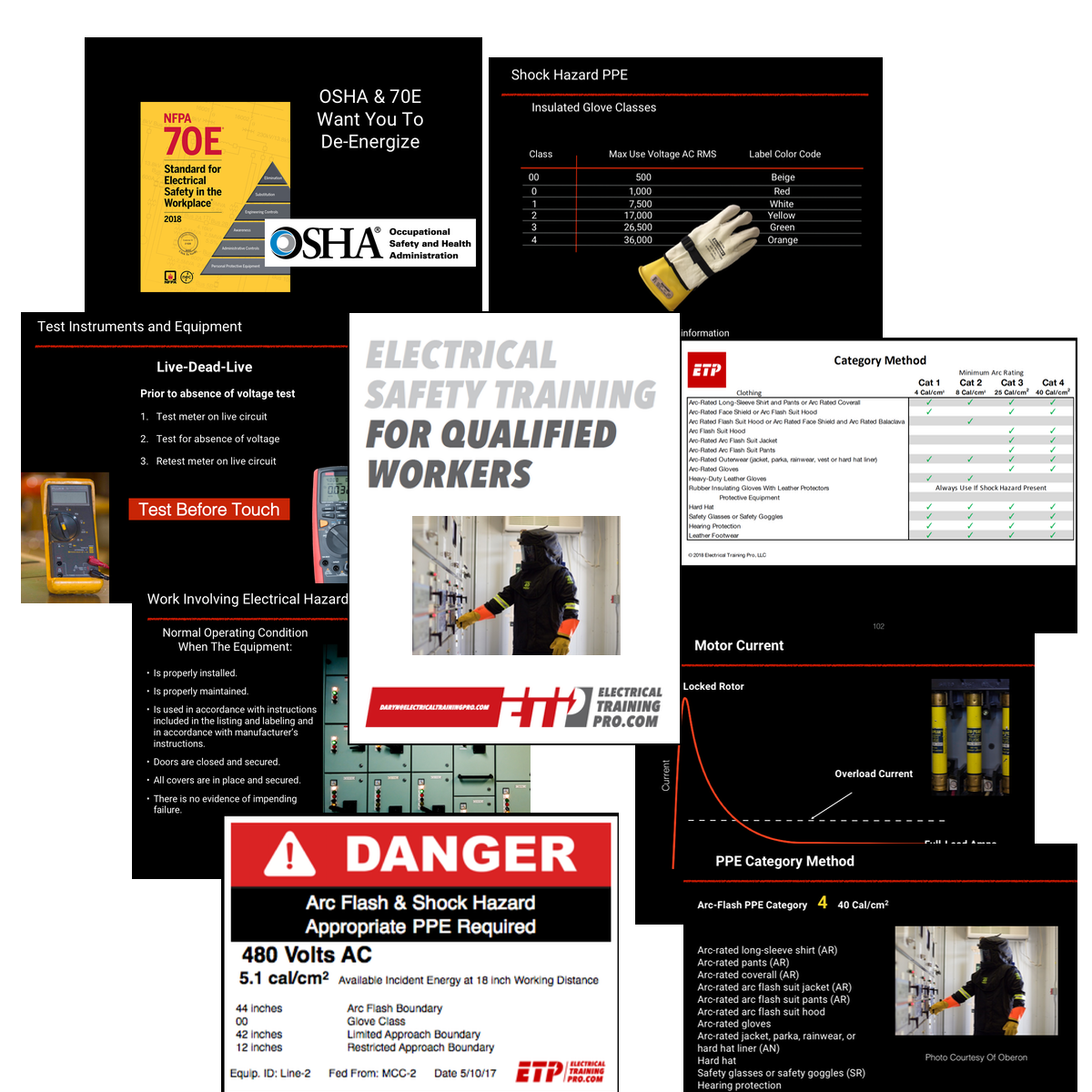
At this point we have every breaker in the panel opened, including the main. We’re not ready to remove the front cover yet because the line side of the main circuit breaker is energized. The line side of the breaker is the incoming power, and a label on the panel indicates it is fed from MDP-3” and off we go to find “MDP-3.”
We go to the upstream main distribution panel “MDP-3” and find a circuit breaker labeled “Panel-A” and open the circuit breaker and put on our lock and tag.
Upon returning to “Panel-A” to begin removing the cover, we must first put up our barricades. The arc flash label indicates that the arc flash boundary for “Panel-A” is 72 inches. The barricades have to be set at least that far from the equipment to prevent workers from wandering into our work area. Instead of using a barricade a second worker can be employed as an attendant to warn others to stop them from approaching too closely. Ideally, use both a barricade and an attendant. If our arc flash boundary was less than the limited approach boundary, which is 42 inches, your barrier could be set as close as 42 inches. Always set the barricade at the first encountered boundary.
You might be thinking we’re not going to need barricades because “Panel-A” is de-energized. “Panel-A” is not de-energized because we haven’t proven it yet. All we know for sure is we have moved the handle on a circuit breaker in the “MDP-3” panel from the on to the off position. You must treat every circuit, wire, panel or piece of equipment as energized until we have proven it isn’t. Always test before touch.
Now, as we are readying ourselves to open the cover of “Panel-A,” we must address what the PPE requirements for this panel are. Part of our job safety plan would be to read the label on the equipment to determine the PPE needed for this panel. We know it is a 480 volt AC panel and we will be crossing the restricted boundary as we verify zero voltage. Therefore Class 00 gloves, which are rated at 500 volts AC, would be needed. They will also be required as we remove the cover as we likely will be within the restricted boundary at that time as well. Many times, as we remove the cover our tools are still in our hands, so we must use insulated tools rated for the voltage.
The tools and gloves have to be inspected daily before each use. In fact, any piece of equipment you use that has insulation, such as power-tool cord, extension cord, meter leads, tools, and the PPE you wear as a garment has to be inspected by you daily before each use. You must remove them from service if they show any sign of damage. The gloves must be electrically tested every six months. As with all PPE, it is essential that they fit the wearer. Don’t make the mistake of buying only one set of gloves for everyone to share. The companies that manufacture or sell gloves have sizing instructions on their websites. Don’t use gloves that are rated for a much higher voltage than you will ever need. If your workers are only going to be working on 480 volts, don’t buy them 1,000-volt gloves.
For arc flash protection we see that “Panel-A” has an incident energy of 13 cal/cm2 with an arc flash boundary of 72 inches.
The Live-Dead-Live Test
We will be performing a “live-dead-live” test. OSHA and 70E require us to verify zero energy at the panel. You must choose an appropriate voltmeter, test it on a known live circuit to verify the meter is functioning correctly. Then, check the circuit we want to work on to ensure it is de-energized, and then retest the meter. If the meter worked properly before and afterward, it was probably working during the test.
Non-Contact Voltage Detector
Non-contact voltage detectors, although very useful for a lot of things, cannot be used for the verification of 0 volts during lockout/tagout. OSHA and 70E both require us to measure the voltage between all phases, that is L1 to L2, L1 to L3, & L2 to L3, and each phase to ground. A non-contact device cannot do that. They work on the principle of capacitive coupling and require a complete current path from your hand holding it through your body to ground.
PPE Required
What Is An Arc Flash
An arc flash occurs during a short circuit in which current flows through an air gap. It could be started by the accidental dropping of a tool, a worker making a connection between an energized conductor and ground or another phase, or with a bad connection in your electrical system. Anytime current is flowing through an air gap it creates tremendous heat that can quickly burn a worker or ignite their clothing. When the initial shorting of the circuit occurs, the current flows through, in this example, a dropped tool. A dropped tool is a sufficient conductive path to cause the short circuit, but it is not a path that can withstand the available fault current. As thousands of amps of current begin to flow through this bad connection, an air gap is created as the tool melts away. The current is now flowing through what is known as plasma, and plasma is a great conductor. As the plasma ball grows, it begins to short out more of the circuit parts. What might have started as a short to ground is now a short circuit of all phase conductors. All of this takes place in milliseconds. The energy from this event is what engineers calculate during an arc flash incident energy analysis. The amount of available fault current, clearing time of circuit breakers and fuses, and other factors determine what this incident energy will be.
Arc Rated Clothing
All arc rated clothing is flame resistant but not all flame resistant gear is arc rated. Clothes made for flash fire, for use in the petrochemical industry, for example, are flame resistant but not arc rated. Electrical workers must have arc-rated clothing.
On the label of arc rated gear, it will have an Arc Thermal Protection Value (ATPV) or an Energy Breakopen Threshold (EBT). ATPV and EBT are both evaluated in the same test, ASTM F1959. The first one to be reached is the reported arc rating. To the end user, it just doesn’t matter which it has. One is not better than the other. The thing you want off the label is the incident energy value or the Category number, regardless if it is ATPV or EBT.
Two Methods For Determining The Arc Rated Clothing Needed
The two methods are the Incident Energy Method and the PPE Category Method. Arc-rated clothing is labeled with both because the manufacturer doesn’t know which you will be using.
You must use one or the other, and you can’t mix them on the same piece of equipment. That is you can’t have equipment with an arc flash label that says it has 19 cal/cm2 incident energy and call it a category two panel. If you have the incident energy on the panel it means you have done an arc flash incident energy analysis and your panel is a 19 cal/cm2 panel and the clothing system worn while exposed will need to have a minimum value of 19 cal/cm2. The clothing category doesn’t play into it at all.
Incident Energy Analysis
This method is one in which electrical engineers have calculated an arc flash energy for your panels based on real data collected from the field. It is typically thought to be the more accurate method, although, because of many factors, predicting arc flash energy is not an exact science. The engineers are relying on your over-current protective devices, your fuses and circuit breakers, to operate as designed. The people collecting the real data from your facility have no way of knowing if the circuit breakers have been appropriately maintained over the many years of operation.
PPE Category Method
This method uses a set of tables to determine what the estimated arc flash energy and arc flash boundary are going to be. This method does not use real-world field data from your facility. It estimates all panels of a particular type to be the same no matter what facility they’re in. To use these tables, you must know the kind of equipment, voltage, clearing time of the over-current protective device, and the maximum available fault current. Finding the voltage and equipment type is easy. Clearing time and fault current are going to require electrical engineers to get involved. The data that will need to be collected, such as wire length, wire size, transformer data, and the calculations the engineers will have to make to arrive at your clearing time and available fault current is essentially the same for doing a full incident energy analysis.
For years many employers have used the tables and ignored the requirements for knowing the clearing time and available current.
When to wear PPE
We are required to use Table 130.5 in 70E 2018 for estimating the likelihood of an arc flash event in the equipment that we will be servicing. The table lists equipment and tasks and indicates the likelihood that an arc flash might occur. This table gives specific tasks, such as Thermography and visual inspections, a pass and says during these tasks there isn’t a likelihood of an arc flash. And further protective measures are not required, including PPE. It also states there are times when the equipment is in the “Normal Operating Condition” that there won’t be a likelihood of an arc flash. Myself, some colleagues in the field, and many of my clients are ignoring this. In our opinion, if the equipment has an arc flash incident energy of 1.2 or above, and you are within the arc flash boundary, PPE should be a requirement no matter what you are doing. And, if an employee is interacting with the equipment, even if the equipment is closed, such as opening or closing breakers, PPE will be utilized. The “Normal Operating Condition” includes a requirement that the equipment is properly maintained and has been used in accordance with the manufacturers’ instructions. How would any employer be able to verify that on a piece of equipment that has been around for many years? In my opinion, you should utilize arc flash PPE indicated by the equipment label any time the equipment doors are open, and you are within the arc flash boundary, and anytime you are interacting with the equipment even if doors are closed.
Your arc flash training needs to include when your facility requires arc flash PPE.
We see the equipment label on “Panel-A” indicates 13 cal/cm2 of incident energy which requires us to wear PPE of at least that arc rating. From table 130.5(G) we see we will need a face shield, hard-hat, balaclava, hearing protection, safety glasses, leather footwear, and because we’ll be within the restricted approach boundary, insulated gloves with leather protectors. We must ensure we aren’t wearing any conductive jewelry and that our undergarments are made of non-melting fabric. The t-shirt you wear under your arc rated clothing has to be made of natural fibers such as cotton. They make arc rated long and short sleeve t-shirts which are ideal for use as an undergarment.
You need to make it clear during your arc flash training, what your PPE procedures are. Does everyone get their own hard-hat, face-shield, and balaclava? Are we using arc rated PPE that we rent or do we own it? Do the employees have to launder it at home and what are those laundering instructions. What about arc flash suits for the high incident energy levels. Where are they kept? One size doesn’t fit all. If one worker is 6 ft 4 inches tall and weighs 250 pounds is going to wear the same arc flash suit as another worker who is 5 foot 7 inches and weighs 130 pounds. No, that won’t work. When a worker is going to exposed to energized work as during verification of zero energy they need to be fully aware of what to wear and where to find it and be comfortable in the knowledge that it is going to be appropriate for their body.
Resources for more information on PPE
Salisbury , Westex, Bulwark, Ariat, Oberon
Your Training
As I’ve said, the employer must provide electrical safe work practices, practices like those in 70E, and then train employees on them. That training needs to be a classroom, instructor-led training that encourages and answers questions. A test of some type and a certificate of completion. Online training should only be used as a refresher course. Your electrically qualified need to be retrained at least every three years.
Document when the training occurred, who was in attendance, and who the instructor was. The contents of this electrical safety training must be documented for future OSHA visits or company safety audits.
Our NFPA70E/Arc Flash Training
Summary
Electrical safety is quite simple. The employer provides safe work practices, trains the employee, and the employee follows them. The employer as well must follow these practices and insist workers priority will always be de-energizing the equipment. The employer also needs to provide proper PPE for the tasks involved. Hopefully, the only energized work, anyone, does at your facility is verification of zero energy during lockout tagout.
This Practical Guide To Arc Flash and NFPA 70E does not cover every detail of the 70E standard. But, hopefully, it will help simplify the standard for those using it in the field.
- Provide electrical safe work practices.
- The centerpiece of those work practices must be the elimination of the hazard. Establishing an Electrically Safe Work Condition.
- Train your people on those work practices. Your electrical safety training, arc flash training is the glue that holds your electrical safety program together.
- Ensure your employees are qualified for the electrical tasks they are about to perform and the hazards for which they are exposed.
- Provide proper PPE for the hazards your people will face. Make sure that PPE fits the individual.
- A qualified worker must conduct a job safety plan and there must be a job briefing prior to work beginning.
- Conduct proper risk assessments prior to work beginning.
You must be logged in to post a comment.